Coded Welding Services and ASME Code Welding Services You Can Trust
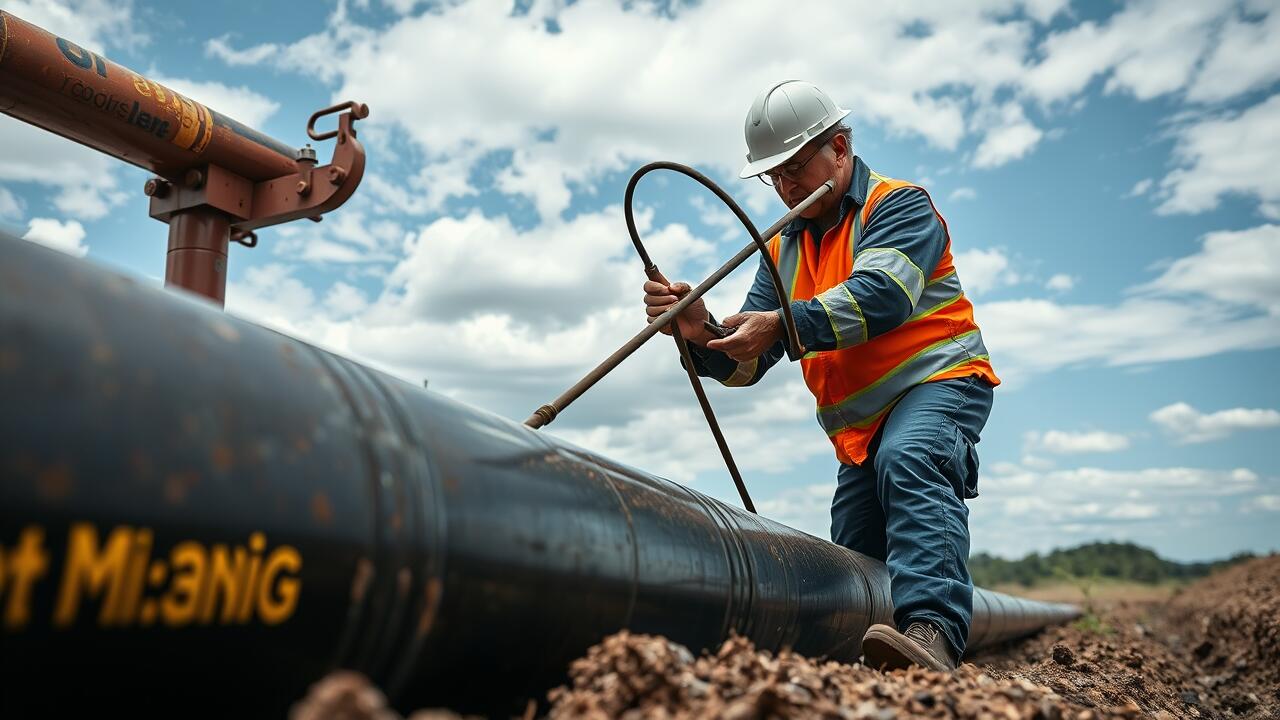
Table Of Contents
Key Takeaways
- Comprehending certified welding offerings
- Varieties of certified welding solutions
- ASME standards in welding services
- Choosing a certified welding contractor
- Uses of certified welding techniques
Understanding Coded Welding Services
ASME Coded Welding services play a crucial role in ensuring the integrity and safety of welding joints across various industries. This type of welding involves specific techniques like gas metal arc welding (GMAW), also known as MIG welding, and tungsten inert gas (TIG) welding, both of which are recognized by the American Welding Society (AWS). Coded welding guarantees that processes such as fusion welding and arc welding meet stringent quality standards, making it essential for sectors that prioritize safety and compliance. The expertise provided through Coded Welding Services reflects an adherence to industry regulations, further enhancing the reliability of structures and products created using these advanced welding methods.
Definition of Coded Welding
Coded welding refers to the process of welding that meets specific industry standards and regulations, ensuring that the welds produced are of the highest quality and integrity. Coded Welding Services often utilize various methods such as stick welding, gas tungsten arc welding (GTAW), flux-cored arc welding, and shielded metal arc welding (SMAW). Each method has its unique advantages and applications, making it essential for welders to be proficient in the techniques that will best serve the requirements of a project.
The importance of welder qualification is fundamental in coded welding. Welders must undergo rigorous training and certification processes to demonstrate their expertise in creating compliant welds. Techniques such as resistance welding further extend the capabilities available within Coded Welding Services, ensuring that welders can deliver reliable joints tailored to industry standards. Employing the appropriate welding methods helps to maintain the structural integrity of critical components in diverse applications.
Importance of Coded Welding in Industry
Coded Welding Services play a vital role in ensuring the integrity and reliability of weldments used across various sectors. Industries relying on precise fabrication processes, such as those involving boilers and pipework, require certified welders skilled in techniques like tungsten inert gas (TIG) welding. These welders possess the necessary certifications to perform high-quality fabrications that withstand rigorous standards. Mechanical engineers often depend on these services to guarantee that the fabricated components meet stringent safety and performance criteria.
The significance of Coded Welding Services extends beyond mere compliance with regulations; it also embodies the commitment to quality and durability in fabrication. Industries such as construction, oil and gas, and aerospace experience enhanced operational reliability through certified welds. Using advanced welding methods, such as TIG welding, professionals can ensure that the welds in complex fabrications can withstand extreme conditions. This commitment to quality ultimately protects both investments and human lives in demanding industrial environments.
Types of Coded Welding Services
Coded Welding Services encompass a variety of specialized techniques tailored to meet strict industry specifications. These services often involve welding materials such as stainless steel and structural steel, ensuring that each weld, including fillet welds, is performed to rigorous standards. Inspections are a critical aspect of this process, confirming that weld integrity aligns with certification requirements stipulated by codes like the ASME Boiler and Pressure Vessel Code (BPVC). Specialized areas may include welding for reinforcing steel, sheet metal, and other metal types, each requiring specific expertise to maintain quality and safety in construction and manufacturing applications.
Overview of Welding Methods
Coded welding methods encompass a range of techniques that are used to ensure compliance with industry standards. These methods include various forms of welding such as shielded metal arc welding, gas tungsten arc welding, and flux-cored arc welding. Coded welding services often require coded welders who are trained to follow specific welding procedures. Each technique may be optimized for different applications, including work on pipe and wire. Companies like WEC Group offer a complete coded welding service, employing multi-coded welding practices to cater to diverse industrial needs.
Specific welding procedures play a crucial role in maintaining the quality and safety of welded structures. Coded welding service providers must adhere to stringent guidelines that dictate the type of materials and methods used in the welding process. Compliance with these standards is essential for ensuring durability and integrity in welds. By implementing code welding practices, businesses can enhance the reliability of their products. Coded welding services provide tailored solutions that meet various operational requirements across multiple industries.
Specialization Areas in Coded Welding
Coded Welding Services encompass various specialization areas tailored to meet specific industrial requirements. Professional welding often involves adherence to stringent guidelines that dictate particular welding processes. Each specialization, such as machinery welding or structural welding, requires an understanding of unique welding procedure specifications. Multi-coded welders are essential in these sectors, as they possess advanced welding capabilities and can execute various welding processes, ensuring the work complies with industry standards.
The demand for ASME welding certification continues to grow, highlighting the importance of specialized skills in modern welding practices. Qualified welding procedure documentation is vital for maintaining safety and quality across different applications. Industries frequently rely on Coded Welding Services to enhance the integrity and durability of structures and machinery. Employing specialists in various welding processes not only guarantees compliance but also improves overall project outcomes.
ASME Code Welding Services
Understanding the intricacies of ASME Code welding is essential for those involved in industrial applications requiring precise and high-quality standards. Coded welding services encompass various techniques, including SMAW welding and GTAW welding, which are integral to the production welding landscape. A multi-coded welder can execute seamless transitions between manual welding processes and automated systems to achieve high welding speeds while adhering to stringent requirements. The versatility of the welding process allows for effective solutions across diverse applications, ensuring appropriate welding quality is maintained. As a popular welding process, code welders play a critical role in industries where reliability and compliance with codes are paramount, emphasizing the importance of using certified coded welding services.
What is ASME Code Welding?
ASME Code Welding refers to welding practices that comply with the standards set by the American Society of Mechanical Engineers (ASME). This type of welding ensures that all welding activities, whether they involve the tig welding process or mma stick welding, adhere to strict quality and safety regulations. Skilled welders are required to demonstrate their competencies through welder qualification records, showcasing their ability to perform tasks including beam welding joints. Code welders hold welder approved test exam certifications, which validate their expertise in executing code-compliant welds.
Coded Welding Services are critical in industries such as manufacturing and construction, where safety is paramount. Full-service welders, such as those certified as Memphis code welders, provide comprehensive solutions to meet ASME requirements. These professionals undergo periodic welder qualification assessments to maintain their certifications. Companies often rely on code-a-weld services to ensure compliance with industry standards, knowing that proficient welders can execute high-quality work while adhering to specific regulations.
Benefits of Choosing ASME Code Welding
Choosing ASME Code Welding ensures that welding projects meet established standards for quality and safety. This approach emphasizes the importance of high-quality welds and the integrity of the weld area. Coded Welding Services under ASME guidelines utilize verified weld processes which provide the assurance needed for both routine and difficult welds. The introduction of new weld procedures within these standards enhances the reliability of pipe-to-pipe weld connections, making these services invaluable in critical applications.
Utilizing ASME Code Welding can significantly improve the overall efficiency and durability of fabricated components. ASME-compliant fabrication services are particularly beneficial for industries where precision and adherence to regulations are paramount. Coded Welding Services provide the expertise required to execute complex welds while maintaining high standards. Clients can expect rigorous testing and documentation, ensuring that each weld—with its high integrity—meets the industry's demanding criteria.
Selecting a Coded Welding Service Provider
Choosing the right provider for Coded Welding Services involves evaluating several key factors. A reputable company should have experienced weld staff proficient in various welding methods, including coded MIG processes. Their fabrication division must be equipped to handle projects such as stainless steel pipework and pipeline fabrication. Attention to detail is essential, especially for small welds that contribute to overall weld strength. Certifications and adherence to relevant codes are critical indicators of professionalism and capability. A well-equipped fabrication facility that can support diverse fabrication projects will enhance the quality of industrial services help offered. Understanding these elements will ensure you partner with a provider who can meet your specific welding needs effectively.
Key Qualities to Look For
Selecting a provider for Coded Welding Services requires attention to several key qualities. Technicians should be well-versed in various fabrication techniques, including those necessary for small-sized weldments. A strong focus on code compliance is essential, as it ensures that welds meet industry standards. A reliable fabrication shop will demonstrate expertise in using materials like cored wire for flat weld repairs and be knowledgeable about various codings to enhance overall weld integrity.
Experience in the fabrication industry is another crucial quality to consider. A provider should not only have a proven track record in Coded Welding Services but also possess relevant certifications that validate their skills. Their ability to handle various types of welds, including those with complex coding requirements, is indicative of their expertise. Thorough assessments of their previous work and customer testimonials can also provide insight into their capabilities and commitment to quality.
Certifications and Qualifications
Choosing a provider of Coded Welding Services requires careful consideration of their certifications. Specific certification demonstrates mastery of code specifications that govern processes like those used in gas pipework and structural code applications. A qualified welder should have the ability to execute techniques such as shield metal arc welding and the creation of fillet weld joints, ensuring both safety and quality workmanship in their projects.
Evaluating a provider's qualifications is equally important. Their experience with advanced equipment technology and familiarity with various machinery can significantly influence the quality of the service delivered. Properly certified professionals in Coded Welding Services are dedicated to excellence, which is essential in high-stakes environments where precision and compliance with industry standards are vital.
- Ensure the provider holds relevant certifications from recognized bodies, such as AWS or ASME.
- Assess the welder’s experience with specific welding techniques required for your project.
- Check for certifications in safety standards and practices relevant to the welding industry.
- Look for evidence of ongoing training or educational development in new welding technologies.
- Verify the company’s history of compliance with regulatory requirements and industry standards.
- Ask for client testimonials or case studies that highlight the provider's past work quality.
- Inquire about the availability of industry-specific certifications that might benefit your particular project.
Applications of Coded Welding
Industries relying on precision and safety greatly benefit from Coded Welding Services. This specialized welding ensures that structures, components, and vessels meet strict industry standards and regulations. In sectors such as oil and gas, power generation, and manufacturing, the ability to design, fabricate, and repair ASME coded pressure vessels becomes essential. Each project involves meticulous attention to detail, including the development of welding procedure specifications (WPSs) and adherence to design calculations. Compliance with ASME codes guarantees that all materials, including 3-mm stainless steel, are subjected to thorough inspections, supported by material certifications and inspection reports. This level of certification not only enhances the reliability of products but also underlines the importance of adhering to high safety and quality standards in the welding industry.
Industries that Benefit from Coded Welding
Coded Welding Services find extensive applications in various industries that demand high standards of workmanship and reliability. Heavy equipment manufacturing greatly benefits from these services, as they ensure that all welded components adhere to stringent regulatory specifications. The use of advanced techniques like gas metal arc welding and tubular wire, along with high-quality materials such as steel electrodes, enhances the structural integrity of machinery. Comprehensive safety procedures paired with regular national board inspections ensure compliance with ASME certification requirements, thus providing peace of mind to manufacturers.
The oil and gas industry also relies heavily on Coded Welding Services due to the critical nature of their operations. Coded welding is essential for creating durable pipelines that can withstand extreme conditions. ASME-authorized inspectors play a crucial role in maintaining quality by scrutinizing welds and ensuring they meet the necessary industry standards. Furthermore, the ability to perform repairs on existing infrastructure using coded welding techniques helps prolong the lifespan of assets, allowing businesses to operate efficiently while adhering to safety and regulatory guidelines.
- Coded welding improves safety and compliance in the aerospace industry, ensuring that all components can withstand the rigors of flight.
- The construction sector benefits from coded welding by ensuring the structural integrity of buildings and bridges, meeting all necessary building codes.
- Shipbuilding relies on coded welding to ensure that vessels are structurally sound and can handle the harsh marine environment.
- Automotive manufacturing uses coded welding to improve the reliability and safety of vehicle components, particularly in high-performance applications.
- Power generation industries implement coded welding to maintain the integrity of equipment used in both renewable and non-renewable energy sources.
- The manufacturing of military equipment benefits from coded welding, which is critical in meeting defense standards for safety and durability.
Conclusion
Coded Welding Services play a critical role across various industries, ensuring that welds meet rigorous standards and specifications. These services encompass a range of processes, including the creation of butt weld joints and the fabrication of vital components like steel beams. Qualified inspectors assess the quality and safety of these welds, confirming adherence to industry codes. The importance of selecting the right services is paramount, as the integrity of structures hinges on reliable and precise welding. By understanding the nuances of these welding processes, businesses can enhance their operations and maintain compliance with stringent requirements.
FAQS
What are the advantages of GMAW welding in the industrial welding process used for ASME coded pressure vessels?
GMAW welding is known for being a versatile welding process that provides high-quality welds, making it ideal for the industrial welding process. This method allows welders to design, fabricate, as well as repair ASME coded pressure vessels, ensuring that competent welder qualifications are met for optimal results. The flat weld—with appropriate techniques—enhances the integrity and durability of the vessels.
How can coded welding services ensure high quality welds in various applications?
Coded welding services are essential in maintaining high quality welds by adhering to strict industry standards and regulations. These services often incorporate advanced techniques and skilled welders, ensuring that every weld meets the necessary quality requirements, which is particularly crucial in applications that demand safety and durability.
How do coded welding services contribute to enhancing the safety and reliability of pressure vessels?
Coded welding services play a crucial role in enhancing the safety and reliability of pressure vessels by adhering to stringent industry standards. These services ensure that welds are performed by qualified personnel and that the techniques used meet the specific ASME codes required for pressure vessels. This attention to detail helps prevent failures and improves the overall integrity of the welded structures, ensuring they withstand operational stresses effectively.
What are some important certifications required for coded welding services in the manufacturing industry?
Coded welding services are essential in the manufacturing industry, and important certifications include ASME (American Society of Mechanical Engineers), AWS (American Welding Society), and ISO (International Organization for Standardization). These certifications ensure that the welding processes meet industry standards and contribute to the overall quality and safety of the manufactured products.
What factors should be considered when selecting coded welding services for critical applications?
When selecting coded welding services for critical applications, it is important to consider factors such as the specific codes and standards applicable to your project, the welding techniques employed, the experience and certifications of the welders, and the quality assurance processes in place. Additionally, assessing the service provider's track record and reputation in handling similar projects can further enhance the confidence in ensuring high-quality welds.